Installing and servicing CPVC the right way
Most common installation mistakes and how to avoid them.

photovs / iStock / Getty Images Plus.



CPVC has been used for residential plumbing in the U.S. for more than 60 years and is unique among today’s plumbing materials. CPVC was specifically designed to be compatible with American drinking water and is impervious to chlorine. As a result, virtually all CPVC failures can be traced back to improper installation or servicing practices.
That doesn’t mean that all failures occur in the first few weeks after the system is installed. CPVC is an extremely robust system that can often withstand the stresses created by some installation errors for years. Here are four installation mistakes that can increase the potential for CPVC failure and how you can avoid them.
Don’t forget the solvent cement
The CPVC solvent welding process is simple, can be performed in tight spaces and creates a bond between the pipe and fitting that is stronger than the pipe itself. But it doesn’t work without the solvent cement.
Dry fitting the system prior to installation increases the likelihood that solvent cement won’t be applied to every fitting. The best practice is to solvent weld each fitting as you go. Inspections can help prevent failures due to dry fits, but the inspector’s job is made more difficult by the lack of contrast between the historically code-mandated yellow CPVC solvent cement and the tan CPVC pipe.
Fortunately, that lack of contrast will soon be a thing of the past. Model code organizations are advancing updates to their codes that allow green-colored one-step solvent cement to be used with CPVC. These changes will be part of the 2024 code and local inspectors have the discretion to approve the use of high-contrast cement today. The product development team at FlowGuard Gold, by Lubrizol Advanced Materials, has taken steps to inform code officials of this development. However, be sure to check with local officials prior to using the new high-contrast cement, which is available from Oatey and E-Z Weld.

Give the pipe room to move
When not properly accounted for during installation, the expansion of a 50-foot run of CPVC resulting from a 100° F temperature change creates about 1,200 psi of force on the pipe. Even CPVC can’t withstand that amount of stress indefinitely.
FlowGuard Gold CPVC expands about 1 inch per 50 feet of straight pipe for every 50° increase in temperature. Expansion and contraction is dictated by the temperature at which the pipe is installed. The pipe will be shorter in colder temperatures and longer in warmer temperatures. In most cases, expansion and contraction can be accommodated with normal changes of direction, but loops or offsets will be required for longer runs. Don’t butt elbows against studs, leave adequate spacing between elbows and hangers/restraints, and follow other manufacturer-recommended practices for accounting for expansion and contraction.
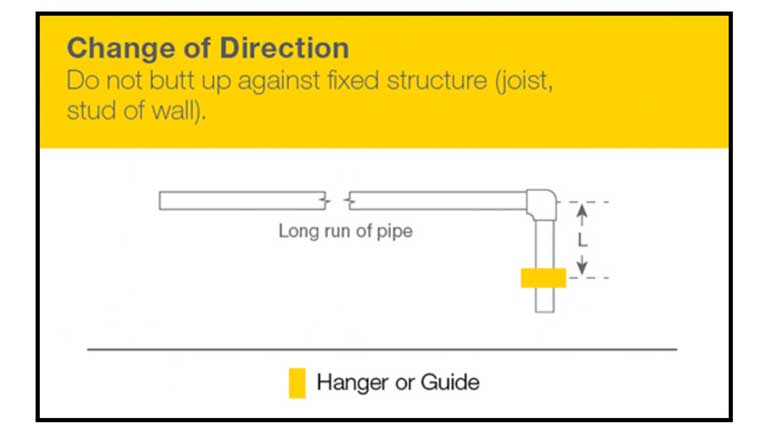
Protect against chemical incompatibility
In any piping system, exposure to incompatible chemicals can lead to premature failure. One example related to CPVC is the plasticizers added to some vinyls to soften them, including those in flexible vinyl wiring and some vinyl-coated hangers. If these plasticizers come into contact with CPVC they will migrate to the more rigid material, softening the pipe. Avoid using coated hangers with CPVC. You can use a wide array of other hangers, including plastic tube talons, suspension clamps and 2-hole strap metal hangers; ensure metal hangers are free from sharp edges and are not overtightened.
If you’re using FlowGuard Gold CPVC, you can reference the FBC System Compatible Program to quickly find what materials are compatible and incompatible with this system. Generic CPVC may have different requirements so check with the manufacturer to make sure you are using compatible materials.
Use the right ancillary products and tools
Remember the old saying about a chain only being as strong as its weakest link? That applies to the ancillary products that support your CPVC system. Ball valves and stubouts are two examples. Use manufacturer-licensed or -recommended ancillary products to ensure proper quality.
Also, be sure to use the right tools when servicing CPVC. CPVC becomes more rigid as it ages. That increases its pressure-bearing capability, allowing older CPVC pipe to remain in service. It also changes the tools you use when cutting the pipe. Where ratchet cutters work fine for new CPVC pipe, they can damage older pipe. Always use C-style tubing cutters, a fine-tooth saw or a wheel cutter when cutting aged CPVC.
Eliminate future failures
Installation errors are no more common with CPVC than with any plumbing system. But because the material does not fail due to exposure to chlorinated water, they account for virtually all the failures that occur. Don’t diminish the performance and reliability benefits of CPVC with improper installation. By avoiding dry fits, accounting for expansion and contraction, using compatible materials, using licensed ancillary products, and adhering to other manufacturer-recommended installation practices, you can consistently deliver reliable plumbing systems regardless of local water conditions — something no other material can offer. To learn more about CPVC installation, take advantage of free resources from CPVC manufacturers, such as web-based training and field checklists.
Looking for a reprint of this article?
From high-res PDFs to custom plaques, order your copy today!