Ensuring corrosion protection beyond routine maintenance in fire sprinkler systems
Corrosion prevention is crucial for protecting lives and property.

Traditional Inspection, Testing, and Maintenance (ITM) protocols are essential but can inadvertently accelerate corrosion rates by introducing fresh oxygen into the system.Image Source: workhardphotos / iStock via Getty Images Plus
Corrosion poses a significant threat in fire sprinkler systems, often remaining undetected until it’s too late, leading to property damage or even loss of life during a fire event. Traditional Inspection, Testing, and Maintenance (ITM) protocols are essential but can inadvertently accelerate corrosion rates by introducing fresh oxygen into the system. Fortunately, advancements in products and strategies offer enhanced corrosion prevention and monitoring capabilities, crucial for protecting lives and property.
Understanding the corrosion triangle
Corrosion in fire sprinkler pipes arises from a chemical reaction producing rust particles. Unlike typical plumbing systems where flowing water flushes away these particles, stagnant water in fire sprinkler systems allows rust buildup, leading to obstructions. This buildup, if present during a fire, can hinder water flow or block sprinkler heads, amplifying the severity of the situation. The corrosion triangle, comprising steel, water and oxygen, forms the basis of this process. Fire sprinkler systems provide ideal conditions for corrosion as all three elements are present. Wet systems, filled with water and oxygen, are particularly susceptible, while dry systems, despite the absence of water, are not immune due to trapped moisture and oxygen.
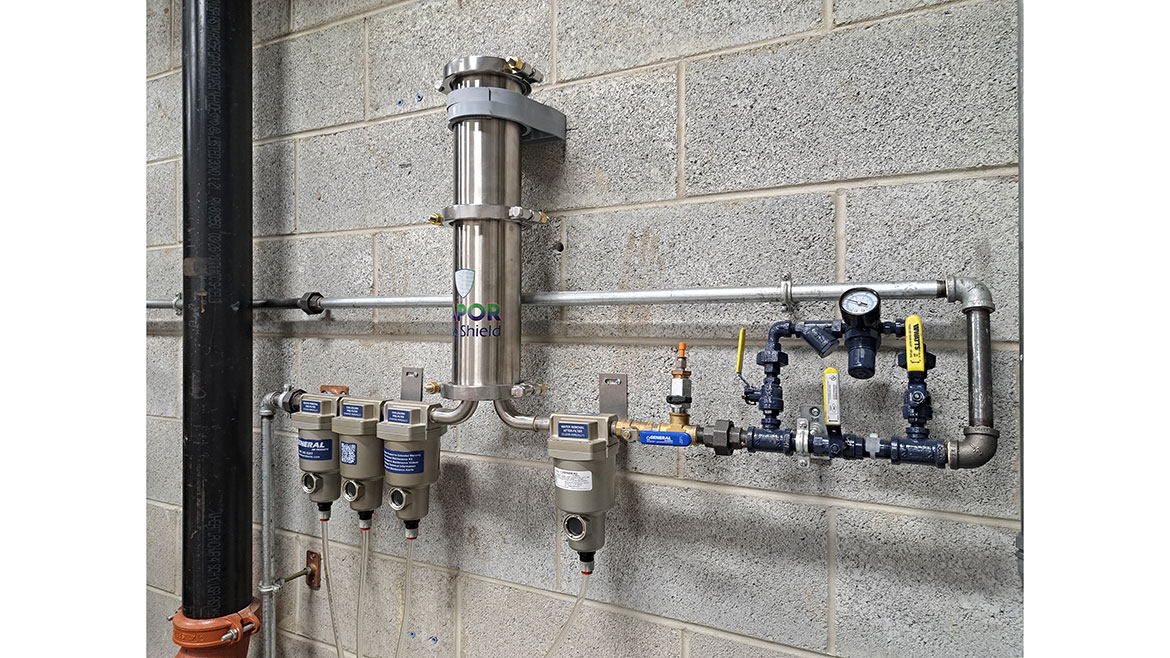
Vapor Pipe Shield by General Air Products is an inline delivery system of Vapor phase Corrosion Inhibitor (VpCI) to prevent corrosion in Dry-Pipe & Pre-Action Fire Sprinkler Systems. Image courtesy of General Air Products
Mitigating corrosion risks
Removing any element from the corrosion triangle halts the corrosion process. While complete removal isn't feasible, effective strategies can significantly reduce corrosion rates. For wet systems, venting air proves beneficial, as demonstrated by long-term studies showing increased pipe life. Dry systems require proper design and installation, including adequate piping pitch and low-point drains to drain condensation and remove water in trapped sections of piping. Additionally, new technologies like “Vapor Pipe Shield” by General Air Products, deliver a corrosion inhibitor throughout the dry system piping, creating a barrier between the steel and water to prevent corrosion.
Role of inspection, testing, and maintenance
Routine ITM schedules aim to detect performance issues early on. However, these activities, particularly in wet systems, can inadvertently accelerate corrosion by introducing fresh, oxygen-rich water. The draining and refilling process during maintenance reintroduces oxygen, fueling corrosion. The presence of oxygen-rich air pockets further exacerbates the issue, especially in high points of the system. To address this, the NFPA 13 introduced requirements for air vents in wet pipe systems, significantly reducing corrosion rates.

PURGEnVENT by AGF Manufacturing is an automatic air vent that releases trapped air in wet pipe fire sprinkler systems to help prevent corrosion and are now required by NFPA 13. Image courtesy of AGF Manufacturing
Reducing oxygen presence
The NFPA's extensive research has identified trapped air as a significant contributor to corrosion in wet pipe sprinkler systems. Their findings underscore the importance of venting trapped air to mitigate corrosion levels. Consequently, NFPA 13 2016 edition mandated the inclusion of air vents in all wet pipe systems constructed with metallic pipes. The advantages of incorporating air vents extend beyond jurisdictions that have adopted this code edition, as they can be seamlessly integrated into new installations or retrofitted into existing systems, thanks to their straightforward installation options.
Manufacturers such as AGF offer a range of manual and automatic air venting valves designed to minimize corrosion while providing versatile installation choices. Installing these valves during the five-year internal obstruction investigation phase can effectively counteract the corrosion triggered by the introduction of fresh oxygen when refilling the system post-investigation.
But what about oxygen dissolved in the water? During scheduled testing of fire sprinkler systems, water flow introduces freshwater rich in oxygen. Utilizing a recirculation system, like those offered by AGF, during testing prevents the introduction of additional oxygen-rich water. This approach not only preserves thousands of gallons of water during testing but also prevents its unnecessary drainage into the public water system.
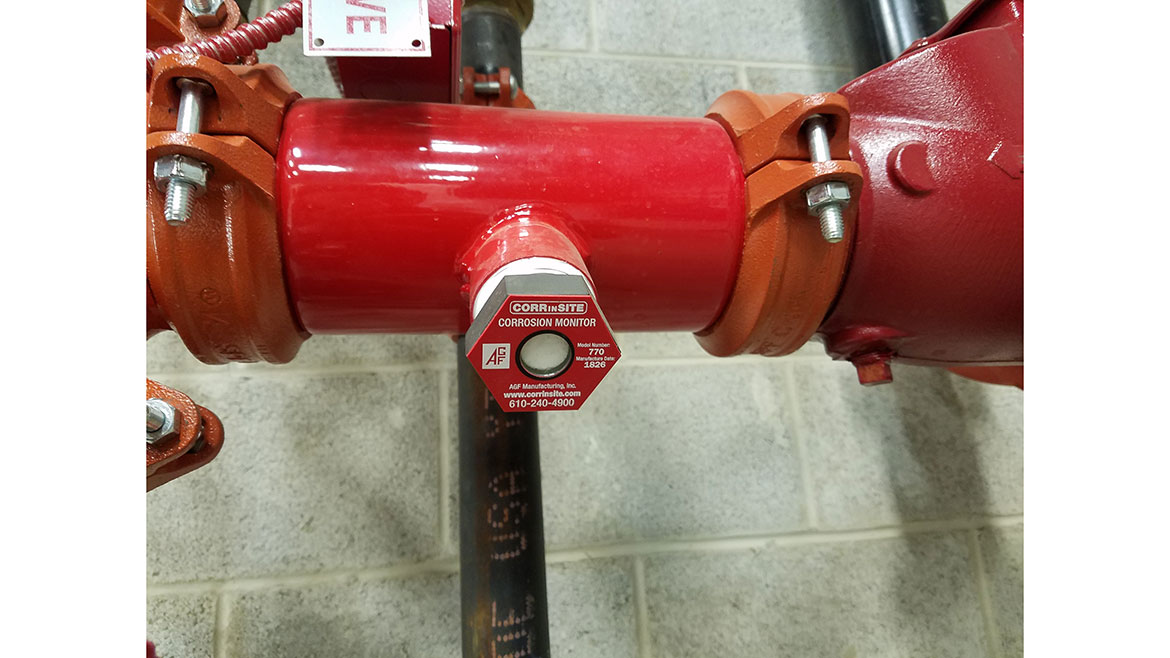
COORinSITE by AGF Manufacturing is a corrosion monitor for dry or wet fire sprinkler systems. The monitor doesn’t require power or coupons and features a sight glass that turns orange when approximately 1/3 of the pipe thickness has been corroded. Image courtesy of AGF Manufacturing
Monitoring and prevention
Proper monitoring is essential to preemptively address corrosion before it escalates. Various corrosion monitors, ranging from powered devices, coupons that need to be sent for analysis, to simple passive monitors, allow facility personnel to track corrosion progression accurately. By staying vigilant and proactive, facilities can intervene before corrosion jeopardizes safety and property.
Taking action against corrosion
Installing air vents, water recirculation systems and corrosion monitors significantly reduces corrosion risks in fire sprinkler systems. Coupled with adherence to scheduled ITM procedures, these measures form a comprehensive approach to corrosion prevention.
Looking for a reprint of this article?
From high-res PDFs to custom plaques, order your copy today!