Heating Perceptions | Scott Secor
A grossly oversized boiler system
Always follow the heat loss calculation.

Image Source: alacatr / iStock via Getty Images Plus
Back in March, I wrote about how the industry has changed regarding warranty issues. We were just issued credits for the two heat exchangers that failed. The shipping costs and the labor costs were not covered. We were told the manufacturer’s representative covered the cost of the two heat exchangers. It took approximately six months for us to get the credits, and the salesman we dealt with tried his best to stay on top of things. I am pleased we received the credits; however, I am not happy they did not cover the labor, the shipping and the materials we had to provide to swap out both heat exchangers. Moving forward, we are still trying to decide if we will continue specifying and installing this brand of boiler.
Last fall, we were asked to look at a boiler replacement project for a town hall. The four existing boilers were condensing cast iron (rare to see this type of boiler these days). Three of the four existing boilers were inoperable due to leaking sections after less than two years of use. The staff mentioned that these boilers were replacements for the nearly identical boilers that lasted less than eight years. The hair on the back of my neck was standing up when we learned they had seven of eight boilers fail within a 10 year period.
While I was at the site in the morning, I tried to play detective and started scribbling notes on my pad. I took many photos at this job, especially the piping, as it was very unusual. I almost filled my canary yellow pad with notes, fearing I would miss something. I measured pipe sizes, looked at all the circulator pump specs, piping methods, cement pad size, insulation thickness, venting, gas pipe and gas pressure, expansion tank(s) and feedwater connection locations, air elimination and separation, piping supports, boiler room access, fresh air makeup, etc.
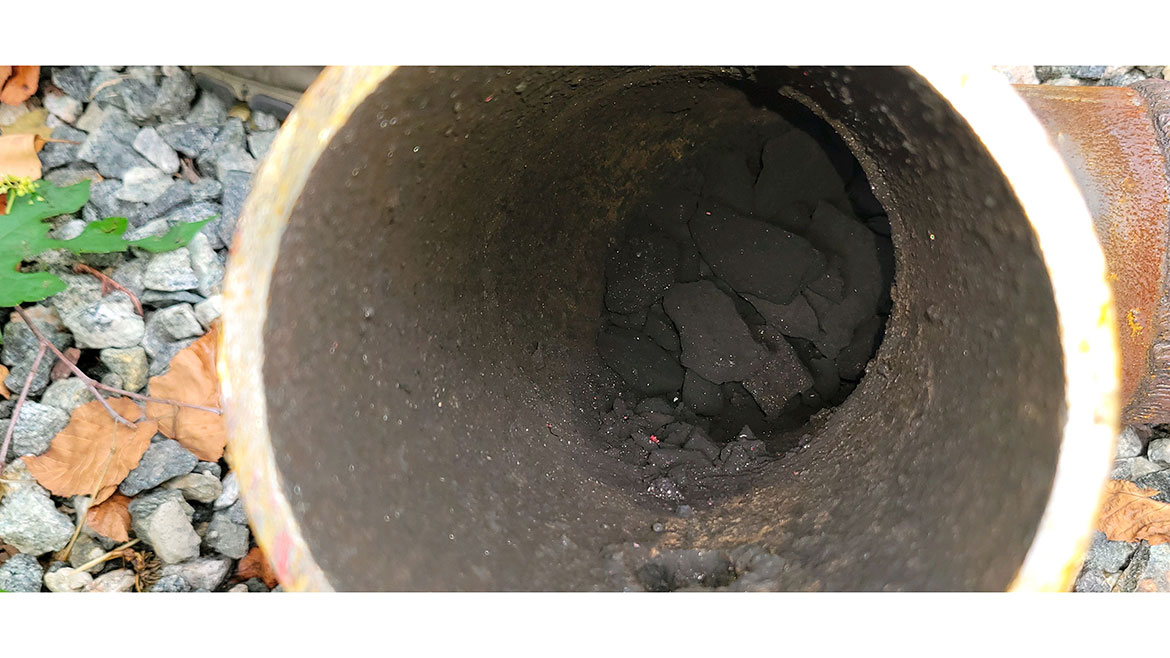
Besides the fact that the boilers were obviously failing prematurely, I wanted to figure out why the piping was so unusual. I scoured the large boiler room for clues. In the corner of the room hidden behind the base-mounted pumps, I found two picture frames hanging on the wall. These frames indicated there were two Cleaver Brooks fire tube boilers installed in 1987. Doing a little math, I gathered the original boilers were replaced after 27 years.
We have visited many boiler rooms over the years with Cleaver Brooks fire tube boilers. We are very much aware that these boilers last a very long time, were very efficient for their time and could be repaired (at a cost) almost indefinitely. On the hot water heating versions, these boilers were able to handle variable flow with ease.
The common 8-inch steel welded piping is about twelve feet above the floor. It had five returns and five supplies for the zones. The zones are the library, town hall, fire department, police department and ambulance squad. The pipes ranged from 1.5-inch for a small zone, up to 3-inch pipe for the three larger zones. It appears that the two original boilers were connected to the header with two short 4-inch flanged supplies and two short 4-inch flanged returns.
Two of the replacement cast iron condensing boilers were tied into one set of flanges and the other two were tied into the other set of flanges. There was 30 feet of 2.5-inch pipe with many fittings on supply from the furthest boiler. The same 30 feet of 2.5-inch pipe with many fittings on the return on the furthest boiler. We were told this boiler (with the least flow) was the first one to fail. The remaining three boilers were piped in a similar fashion, just slightly closer to the common flanges. The boilers were not piped primary/secondary or according to the current installation manual.
On the drive back to my office that afternoon, my hands were cramping from all that writing. At the same time, my head was spinning with ideas. After fighting traffic for almost two hours on the New Jersey Turnpike, I finally made it back to my office. I gazed over my photos and my notes. Based on a hunch and the circulator pump data I jotted down earlier; I immediately realized the boilers were grossly oversized. The system pumps and pipe size would indicate the system requires somewhere between 3-4 million Btu of input. Yet, there were four boilers with a total input of 8 million Btu. We decided to do a preliminary heat loss calculation using our notes and photos combined with Google Earth software. The actual heat loss was only 2.6 million Btu on the coldest day of the year.
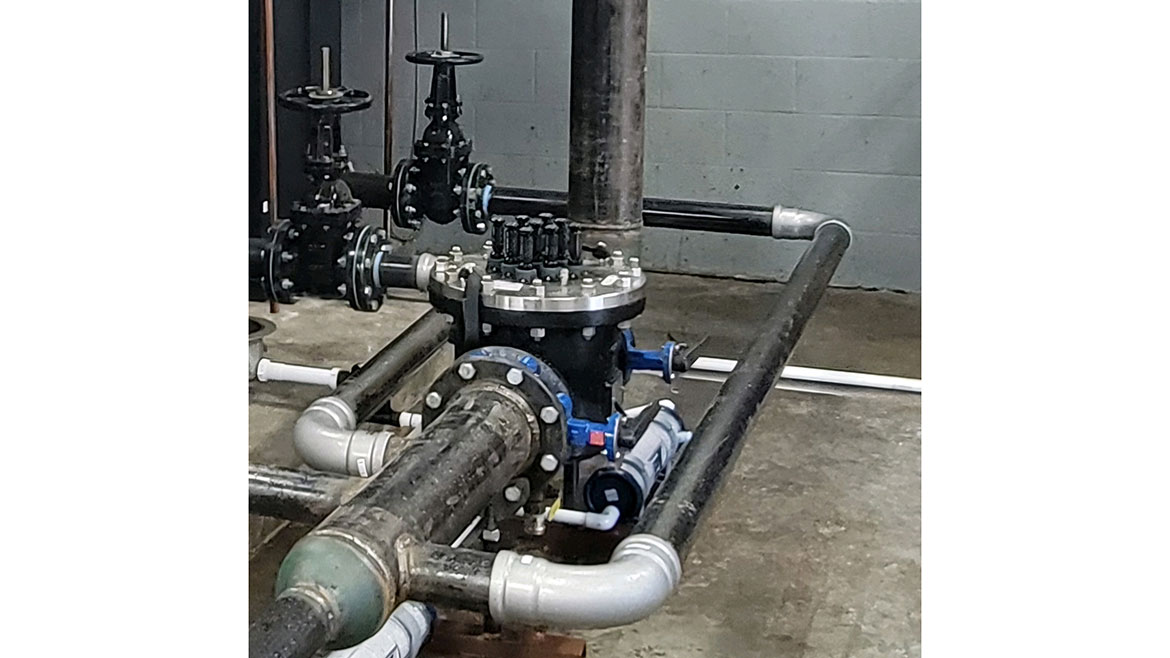
The following day I sent an email to the general contractor we were working for. I told him that we should replace the four existing 2 million input Btu boilers with three new 1 million Btu input boilers. Since it was such a critical building, maybe four boilers instead of three in case one crapped out on a bitterly cold day. He said he would consider my suggestions and talk to the engineer. I knew the smaller boilers would better match the load and reduce pipe sizes, short cycling, upfront cost and utility costs, etc.
The next day, I was told they would be replacing the boilers with four new boilers, rated at 2 million each, just like the existing boilers! I have tried arguing with engineers and architects since I started in the business in the 1980s. I have learned to do what the engineer says and not bother arguing. This GC supplies the boilers for all of his jobs, and as such, he also supplies the warranty.
Before we had the old boilers and near boiler piping removed, we noted there were some issues with two of the zones that were added since the original installation almost 50 years ago. Others tied these two returns into the supply main instead of the return main. When we drained these two zones, they were almost filled with black mucky water. We can only assume that there was very little to no flow in these areas. When we reconfigured the piping, we made changes and tied these two zones to the return instead of the supply. We also noted that the roughly 10-foot section of 8-inch pipe we removed was filled about one-third with black thick muck, about the consistency of mayonnaise.
We have recently completed the installation of these four boilers. Oddly, the engineer had no plans for us and suggested we follow “normal” piping practices and follow the manufacturer’s instructions. We decided to use the primary/secondary piping method. The main system piping and air separator is 8-inch welded steel pipe. Boiler common piping is 6-inch welded pipe, and each individual boiler is piped in 4-inch steel. Each boiler has a dedicated inline low head high volume circulator.
The next day, I was told they would be replacing the boilers with four new boilers, rated at 2 million each, just like the existing boilers! I have tried arguing with engineers and architects since I started in the business in the 1980s. I have learned to do what the engineer says and not bother arguing. This GC supplies the boilers for all of his jobs, and as such, he also supplies the warranty.
When we performed a hydrostatic test on the new boilers and the new piping, we were pleased to find no leaks. We rinsed all new piping along with the air separator (with strainer) and the near boiler piping by opening the fast-fill bypass piping. Thankfully, the water went from filthy to clear after an hour or so. Once were convinced the water was clear and the strainer was clean and thoroughly flushed, we opened the isolation valves that went out to the building and turned the circulator pumps on to move the water through the entire system. After another hour, we dumped the base-mounted pump strainers and the air separator strainer. This time, we found very little black murky water. Thankfully, the GC agreed to have us install a six-inch magnetic separator on the inlet piping to the four new boilers. I suspect the magnet will be working overtime on this system.
Finally, we were told the system was filled with an antifreeze solution less than two years ago. As such, we had to be extra cautious not to dump the entire system. The maintenance director mentioned the cost for the antifreeze with the labor to pump it into the system was over $30,000. We strongly suggested (in writing) that the boiler chemical people test the boiler water for solids, chlorides, hardness and anti-freeze levels before the system is put into operation.
Looking for a reprint of this article?
From high-res PDFs to custom plaques, order your copy today!