Duel-fuel solution offers best of both worlds
January 7, 2025
Duel-fuel solution offers best of both worlds
January 7, 2025Image courtesy of Mosey Photography
Shortly after Keefer Rader wrapped up his most recent air-to-water heat pump installation, two feet of snow fell at the customer’s house.
Rader’s company, Outlaw Mechanical, has built a reputation as one of the leading boiler experts in the high-elevation bedroom communities surrounding Albuquerque, New Mexico. In recent years, he’s expertly expanded that reputation to include hydronic heat pumps.
“We’re still very much in the boiler business, but I saw the trend toward heat pumps and knew I’d eventually have to embrace it,” he says. “Customers were starting to ask about heat pumps, and I wanted to be the guy with the answers.”
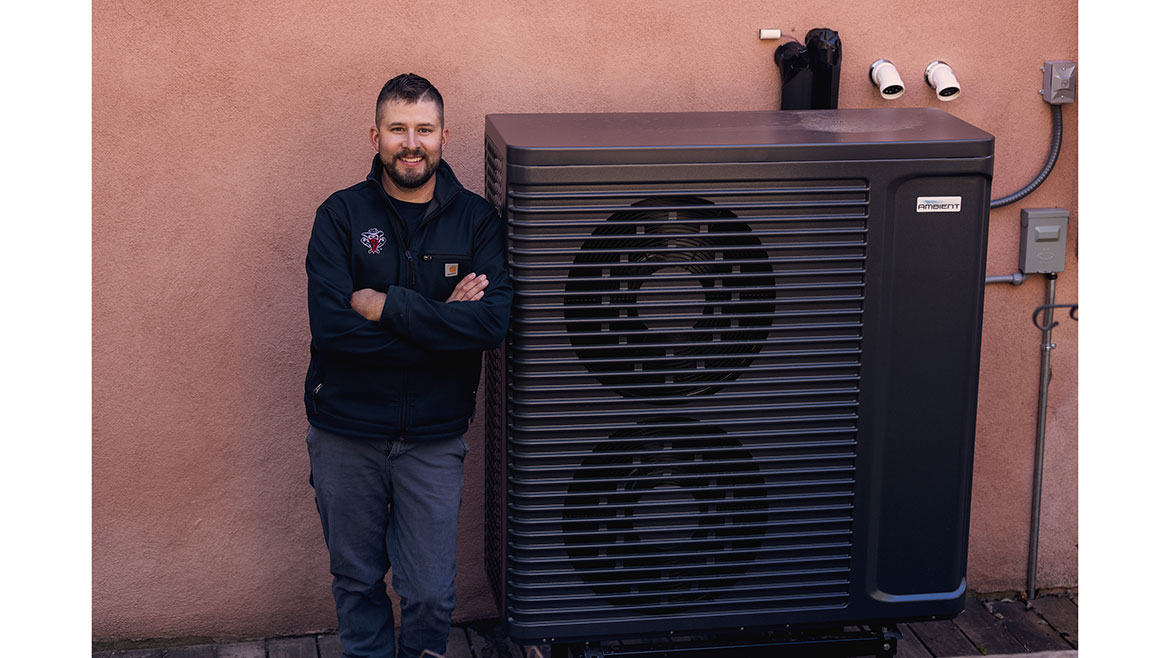
Keefer Rader, owner of Outlaw Mechanical. Image courtesy of Mosey Photography
Outlaw Mechanical installed its first hydronic heat pump in 2020. Rader’s frustration — similar to those among many hydronic experts across the country — was that he couldn’t find a manufacturer of quality heat pumps that produced an entire package. Typically, he’d have to pair outdoor and indoor units from different brands, then find a control that fit.
In fact, the owner of Outlaw’s very first hydronic heat pump referred a neighbor in mid-2024.
Ideal for dual-fuel
“The homeowner called me to ask about an electric heat source for his home,” Rader says. “I visited the property and came away thinking that — though there were a few hurdles — the home was ideal for a hydronic heat pump.”

Keefer Rader, owner of Outlaw Mechanical, has installed several air-to-water heat pumps in and around Albuquerque, New Mexico. Image courtesy of Mosey Photography

Outlaw Mechanical installed two Alta condensing boilers in addition to the Ambient heat pump: one to supplement the low-temperature water zone, and one for high-temp radiant and DHW. Image courtesy of Mosey Photography
The 3,800-square-foot, semi-passive solar home is built into a hillside, with the lower level heated by in-floor radiant. The upstairs features fin-tube baseboard. There’s also a 10,000-kW photovoltaic solar array on the property.
Rader learned that the circa-1998 radiant system is piped with polybutylene tubing. This came as no surprise.
Looking for a reprint of this article?
From high-res PDFs to custom plaques, order your copy today!
“Polybutylene was used extensively as radiant tubing in the Southwest through the early 2000s,” Rader says. “In a best-case scenario, those hydronic systems became oxygenated. I knew we’d have to isolate those zones from the heat source in order to keep the systems in operation.”
The homeowner wanted very much to electrify the heating system. Their existing solar array made electrification even more attractive. The owner used solar energy during AC season, but never for heating.
Originally, two cast iron, LP-fired boilers served the home. One unit served the low-temp system downstairs and one served the fin-tube zones upstairs; nine zones in all, plus DHW.
“I explained that we could heat the lower level of the home with a heat pump,” Rader says. “However, given the high water temperatures needed upstairs, a heat pump wouldn’t produce water temperatures high enough for the fin-tube zones on a design day.”

Rader installed Taco accessories for circulation, zone control and air elimination. Image courtesy of Mosey Photography
Dual-fuel solution
Rader suggested using U.S. Boiler Co.’s Ambient air-to-water hydronic heat pump and dual-fuel package, allowing the home to switch from electric to LP automatically and as needed.
In many cases, the Ambient heat pump package can overcome low ambient temperatures with backup resistance heat instead of relying on a fossil fuel boiler for backup. However, the home’s 200-amp service was already tapped for home appliances. With the high-temp zones and DHW production to account for, the home would still rely on LP to some degree.

A Taco 4900 Air Separator was installed to eliminate oxygen from the closed-loop portion of the heating system. Image courtesy of Mosey Photography
Rader’s design began with the Ambient heat pump. It’s capable of supplying up to 140° F water and can operate with outdoor temperatures as low as -13° F. That’s far beyond the 120° F supply temperature Rader needed at an outdoor design temperature of 12° F.
“The Ambient heat pump is well built,” Rader says. “It’s a lot heavier than other brands I’ve worked with before. The weight is only a hassle for a few minutes. If that means it’ll last longer, I’ll take it. It’s also simple inside, and the dual-fuel controller makes connecting to the rest of the system a breeze.”
To this, Rader added an Alta condensing boiler and an Alta condensing combi-boiler. The 200 MBH combi provides DHW and backup heat for the six radiant zones.
“The heat pump will provide water temperatures between 90° F on the low end of the curve and 120° F on the high end of the curve,” Rader says. “I’ve found that a 30° F span is ideal for a reset curve in our area. In the event that outdoor temps exceed the heat pump’s capacity, the dual-fuel control will fire the boiler.”
The 80 MBH boiler is dedicated to the three zones of fin-tube baseboard upstairs. It modulates on a reset curve between 150° F and 180° F.
The boilers were vented with schedule 80 CPVC through the existing B vent, up two stories, and out the original chimney. Combustion air piping was drilled through the first-floor wall. Outlaw Mechanical completed the entire retrofit in five days.
Mastering the retrofit: tricks of the trade
Rader’s experience allowed him to avoid three potential pitfalls on the project. The first was the oxygenated radiant loops. If allowed to pass through the boiler and other components, this water would either destroy system components or create deposits.

Image courtesy of Mosey Photography

Rader connects the Alta boiler to the USB-Connect Bluetooth app in order to set boiler setpoint temperature. Image courtesy of Mosey Photography

Rader uses a small, point-of-use electric water heater to overcome standby heat loss across the domestic hot water recirculation loop, ensuring that the combi boiler only fires when there’s a call for DHW. Image courtesy of Mosey Photography
His fix was to isolate the entire radiant system from the heat pump/boiler loop by installing a 200,000 Btu Taco brazed-plate heat exchanger. The load side of the heat exchanger is circulated by a 0015e3 pump set to medium.
Next, Rader wanted to increase the efficiency of the domestic hot water recirculation system. In large homes with long recirculation loops, water inevitably cools as it stands and moves through the lines.
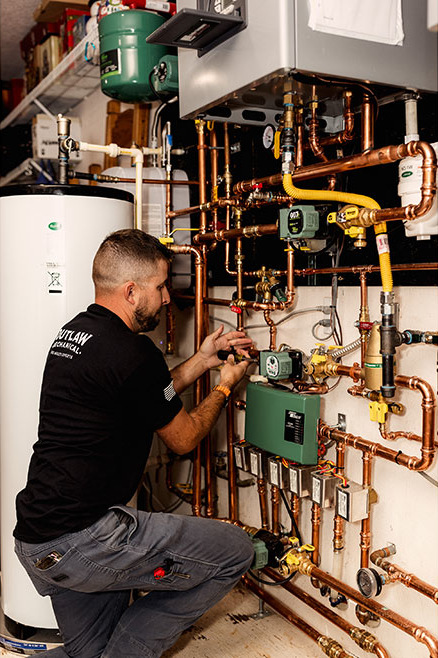
Rader changes the speed setting on a Taco 0015e3 circulator. Image courtesy of Mosey Photography

Outlaw Mechanical is known around Albuquerque as the “boiler experts” and they’re quickly gaining the same reputation for their expertise in hydronic heat pumps. Image courtesy of Mosey Photography
To minimize standby loss, he added a Taco SmartPlug to the 006e3. The SmartPlug has several intelligent modes to best fit a home with a tank-style water heater, but Rader installed a combi-boiler for DHW production, so he took the system a step further by installing an electric tankless Eemax water heater in the mechanical room. The small water heater is typically installed at point-of use, but Rader used it to overcome the recirculation loop’s standby loss. As a result, the combi only fires when there’s a call for DHW.

The Ambient heat pump system includes a dual-fuel controller, ensuring that it’s easy to pair the hydronic heat pump with a boiler. Image courtesy of Mosey Photography
“I’ve been installing the Alta condensing boiler because the gas-adaptive technology was a big benefit considering most of the homes I serve are between 5,000 and 10,000 feet above sea level, so derating the boiler is as simple as selecting an altitude range in the USB-Connect Bluetooth app. I’ve installed 30 Altas this year alone.”
Learning curve
The homeowner was very impressed with the craftsmanship of the system and was surprised by how quiet the heat pump operates. There was, however, one learning curve Rader had to help the customer overcome.
The radiant zones used to circulate at 140° F at all times, regardless of the outdoor temperature. The floors were hot to the touch and it caused boiler short-cycling.
Now, the in-floor system circulates at 120° F at most, and the floors are warm, not hot. Naturally, the question of whether the system works came up in conversation.

Outlaw Mechanical is known around Albuquerque as the “boiler experts” and they’re quickly gaining the same reputation for their expertise in hydronic heat pumps. Image courtesy of Mosey Photography

The owner of the passive solar home wanted to electrify his heating system in order to benefit from solar photovoltaic year-round. Image courtesy of Mosey Photography
“The owner is a bright guy,” Rader says. “I asked him if the system was maintaining his room setpoint temperature. He said it was. I didn’t have to explain it any further.”
“I reminded him that he asked for efficiency, and one of the ways to achieve higher efficiency is to lower the water temperature,” Rader concludes.
The home is now more comfortable than it’s ever been, the system is quieter, and the customer is using less fossil fuel while fully capitalizing on his solar array investment.