Radiant Forum


Sand Vs. Concrete
Q: How about using sand or pea stone instead of concrete for a radiant thin-slab installation?Answer: This question has come up on several occasions. The person asking it usually is thinking there must be a simpler way of making a radiant thin-slab compared to pouring concrete or gypsum underlayment.
The usual proposed concept is to install wooden 2x2 sleepers spaced 16 inches apart, staple the tubing down to the subfloor between them, then fill in the space with sand or pea stone.
Sounds simple enough, doesn't it? Just dump the loose aggregate on the floor, rake it around a bit, then drag a plank over the sleepers to level it off.
Unfortunately, this type of installation is likely to be problematic for a number of reasons. First, dry sand has a much lower conductivity than either concrete or poured gypsum underlayment. According to the sources I referenced, dry sand has about 1/6 the thermal conductivity of cured concrete. When I ran these numbers through a thermal simulation, it predicted the output of the “sand slab” floor to be about 43 percent of the concrete thin-slab with all other factors equal. That's a major case of thermal constipation where the heat simply can't transfer away from the tube at a reasonable rate.
Secondly, I can't imagine trying to keep the sand or pea stone off the top of the sleepers as the cover sheet or wood flooring is installed. Every time you put your foot down, some of the sand or stone would move around.
Finally, in a short time the loose aggregate would settle, leaving an air gap under the materials installed above it. This adds even more thermal resistance to the picture.
Every installation that I've heard about where this approach has been tried has not resulted in satisfactory performance.
Do yourself a favor: Play all you want with the sand at the beach or in your kids sandbox, but when it comes to radiant floors, stick with proven slab materials such as concrete and gypsum underlayments.
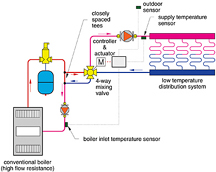
Magic Number
Q: Should I use a three-way or four-way motorized mixing valve for a radiant floor application?Answer: When properly piped and controlled, either one can do the job of providing the proper supply water temperature as well as protecting a conventional boiler from sustained flue gas condensation.
The three-way valve only creates one mixing point, and this point is used to prepare the supply water temperature. Protecting a conventional boiler from flue gas condensation requires a second mixing point. This is where the cool return water from the floor circuits is mixed with hot “bypass” water from the boiler. For the system shown in Figure 1, this mixing takes place within the primary loop tee labeled (B). For both mixing points to operate properly, there must be two circulators in the system.
This two-circulator arrangement is not always required if a four-way motorized mixing valve is used. In systems where the head loss of the boiler is very low and the four-way mixing valve is located close to the boiler, a boiler circulator is not necessary, as shown in Figure 2.
Flow through the low head loss boiler circuit is created by the pressure drop and momentum exchange within the four-way valve. This arrangement, although common in European systems, is often overlooked in North American systems.
A warning is appropriate: When using low-mass boilers or boilers with significant head loss, a boiler circulator should always be used in conjunction with a four-way valve. The suggested piping is shown in Figure 3.
Looking for a reprint of this article?
From high-res PDFs to custom plaques, order your copy today!